On most orbital welding power supplies, there are two primary options when it comes to orbital welding programming – the continuous program and step program. It is important to know how these two programs work, where lies the difference, and why you might choose them for your automated tig welding application.
What Does an Orbital Welding Program Look Like?
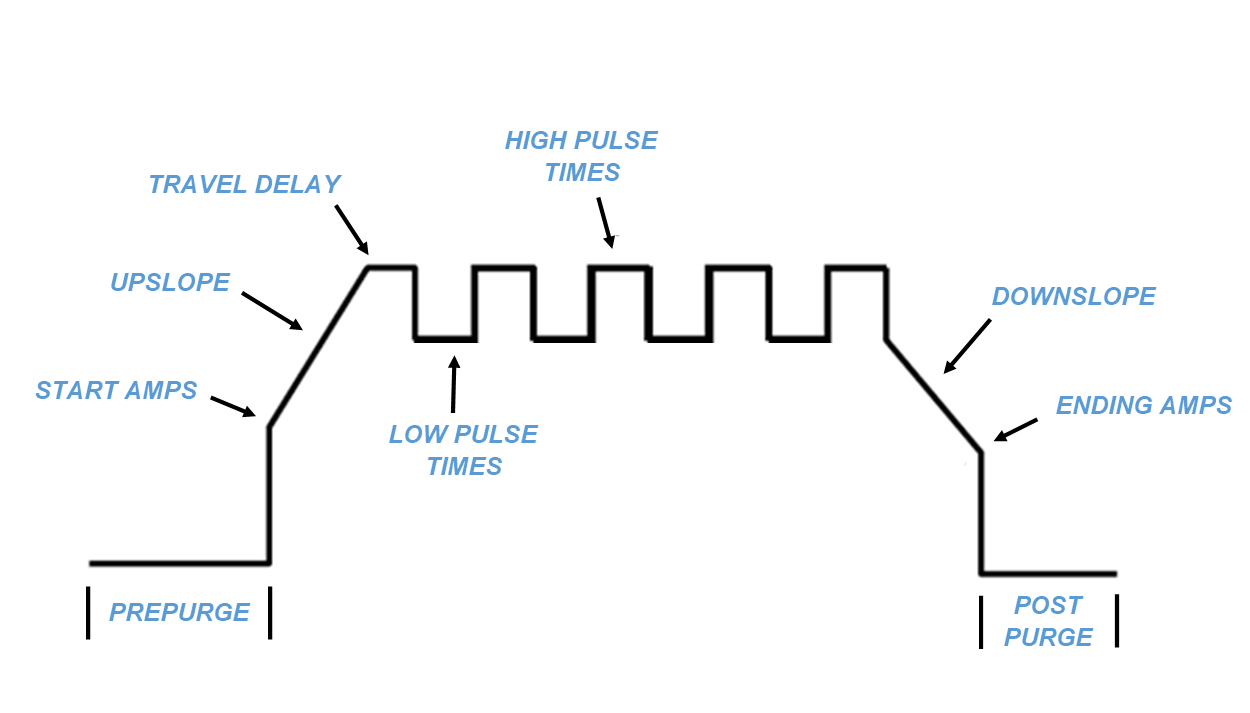
No matter which program you choose, orbital welding is consistent in its overall process. The ceriated tungsten electrode mounts on the rotor of the weld head. Depending on the weld head manufacturer, the weld head will start at the 3 o’clock or 9 o’clock position. Purging is initiated to expel any remaining oxygen. After the prepurge, the arc strikes and goes through a “rotation delay”, otherwise known as a “travel start delay,” where the tungsten stays in place while the weld puddle is established, and the desired penetration is achieved.
From there, the rotor starts to move or “orbit” around the piece. This is either done in a continuous or step fashion – which we will explain below. During the orbit, the arc alternates between high and low pulses in most applications. This pulsing action which helps keep the puddle cooler and the penetration more consistent.

When the electrode travels 360 degrees around the tube/pipe it will then continue another 10 degrees to give the weld a good “tie-in” or “overlap”. It will then go into what we call the “downslope”, this is when the head will slowly bring the amps down giving the weld puddle a tear drop or dovetail effect thus closing the puddle and not allowing any deviations or weld defects at the end of the weld, most downslopes are somewhere between 4-12 seconds depending on the OD of the tube/pipe. Once the downslope is complete, the arc shuts off and the head purges argon for 15-30 seconds. This helps with the color and cooling process of the metal. Then, the weld is considered complete.
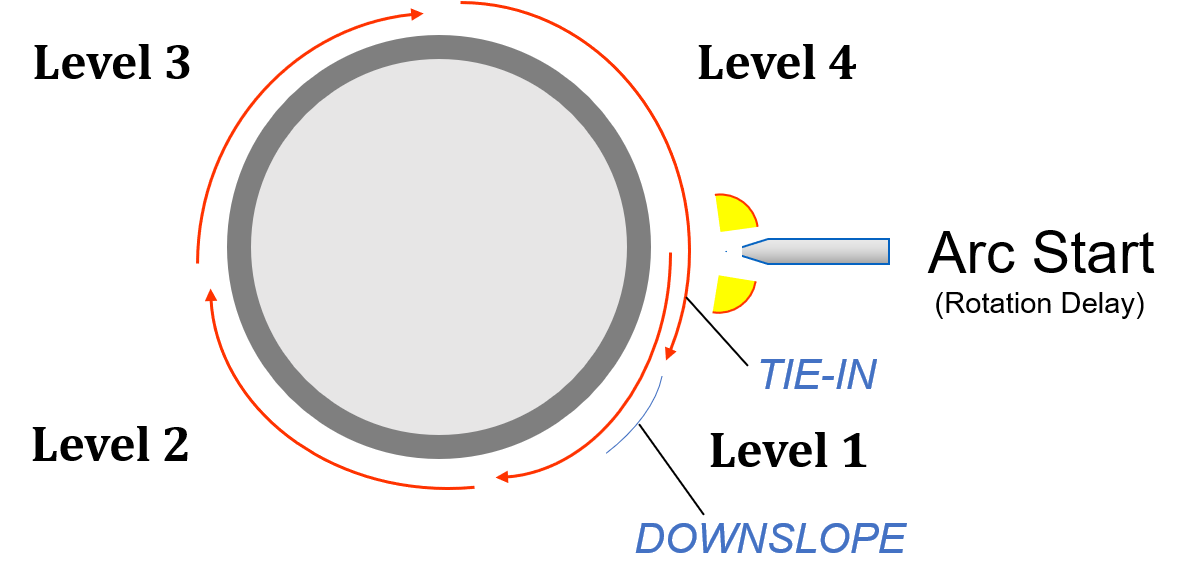
Continuous Weld Program
When it comes to orbital programming options, continuous is the go-to for sanitary tube welding applications.
What do sanitary welding applications look like? Most commonly, they are in critical welding industries such as food, dairy, pharmaceutical, aerospace, and more. These industries often have rigorous weld inspection standards and use orbital welding as a solution.
Sanitary tubing is commonly thin-walled stainless steel tube, typically between .035” and .065” wall thickness. Continuous programming is ideal for applications using tubing within this size range. However, in some applications in larger diameters such as 4” and 6” in .083” thickness, users can choose between continuous and step programs.
Continuous programming is done with the process detailed above. Purge – Arc Start – Upslope – Pulsing – Tie In – Downslope. The difference lies within the rotation motion within the pulsing step. In a continuous program, the rotor moves in a continuous motion, never stopping during the 360-degree orbit around the tube or pipe. As the tungsten and subsequent arc move around the piece – the amperage continually decreases.
Step Weld Program
The step program allows the welder to penetrate heavy wall tube/pipe without having to use the high amperage needed if using a continuous program. The step program is much like slowing down your weld speed instead of turning your amperage up if you are hand TIG welding.
A step program would be used on heavier wall tubing (.083” or heavier) or most primarily schedule 10 SS pipe applications. Additionally, you would use it on dissimilar material or mismatch fit up.
While the continuous program consists of a steady movement around the piece, a step program differs in which it makes repeated stops throughout its rotation - much to the likeness of the second hand of a clock. When a step program is performed, the tungsten rotates during the low current pulse (or background amps) and comes to a stop during the high current pulse (or primary amps).
The stopping of the tungsten during the high current pulse promotes deeper penetration on the heavier wall tube/pipe without the need to increase amps. This also reduces the heat-affected zone of the weld and promotes a more stable weld arc, thus giving you a more consistent and repeatable weld.
FOR EXAMPLE: You are welding 2” schedule 10 SS which has a wall thickness of .109”. If using a continuous weld program, you would most likely have a high pulse current of around 110 amps and a low current pulse of 33 amps to get the desired penetration for a successful weld. If using the step program, you can drastically reduce the high and low pulse amperage, typically by 15% to 20%.
The benefits of using the step program in this example will be achieving the desired penetration, a decreased heat-affected zone, and a more stable arc all while promoting a consistent and repeatable weld.
Interested in learning more about orbital welding programming? Contact Morgan Industrial Technology for a detailed equipment demonstration or orbital welding training session. Rely on MIT as your knowledgeable, orbital welding resource center.
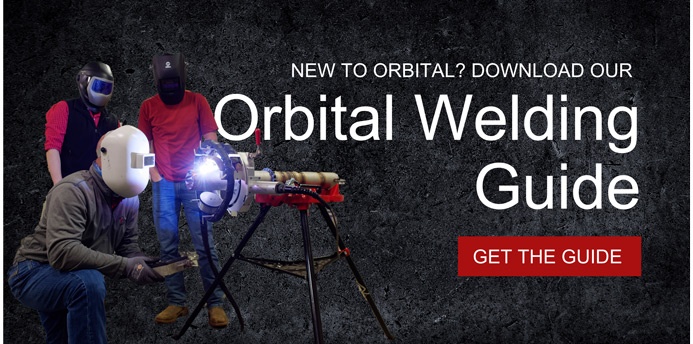
Tags:
Feb 17, 2021 12:00:00 AM
Comments