Sugaring isn’t sweet when it comes to welding. Though oxygen can often be thought of as a life-giving resource, it can also be the cause behind a failed weld.
Oxygen greatly compromises the integrity of welds. The presence of oxygen during your weld can cause discoloration and can lead to eventual corrosion and rust. This process of oxidation on the back of your weld is often referred to as “sugaring”, which often looks like a splatter of granulated sugar – hence the name. Stainless weld sugaring causes the buildup of the materials running through a product line and is a breeding ground for contaminants and bacteria in process piping industries.
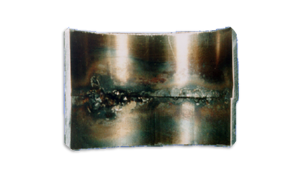
How to Avoid Weld Sugaring
To avoid this, we suggest purging the piece of all oxygen before welding. To purge tube and pipe, MIT suggests using purge plugs. This purging process evenly diffuses an argon gas mixture, while expelling the remaining oxygen out of the enclosed environment.
In orbital welding, sugaring can be detrimental to your operation and lead to costly fixes. One way to avoid these issues is to use an oxygen analyzer to detect and measure the oxygen levels within the enclosed environment. Oxygen analyzers can measure down to 100 ppm (parts per million). The orbital welder operator can use this tool to measure and confirm the oxygen is at an appropriate level before striking an arc.
Including this optional step in your orbital welding process can help to ensure success and lower the risk of error in your project. One application where you should consider an O2 analyzer is while welding extended lengths of tubing. For example, if you are welding a joint with a 100 ft long tube, you might not know when your purging gas has gotten to the joint. An oxygen analyzer can take the guesswork out of the equation. Some applications, especially in high-purity work, require the use of an oxygen analyzer before performing the weld.
Oxygen Analyzers for Welding Stainless Tube and Pipe
If you’re interested in using an oxygen analyzer for your application, we suggest the Pro OX-100B or the Purge Eye 100 IP65.
The PurgEye 100 IPS65 will indicate oxygen levels from 20.94% down to 100 ppm (0.01%). The tool itself is dustproof and waterproof. You can also calibrate your own monitor at any time without having to return it to the factory. The PurgEye 100 will provide immediate and more importantly – accurate readings for your tube or pipe welding application. At an oxygen level of 2%, its accuracy level is within ± 0.02%.
The Pro OX-100B has unlimited data logging capabilities in real-time as well as Bluetooth transmitting. It has a color notification system based on the oxygen levels users specify, making it easy and quick for operators and inspectors to understand, reducing the chance of error. Its accuracy levels are within ± 0.01%.
Tags:
Stainless Steel, Sanitary Welding, Purging, Orbital Welding Supplies, Orbital Welder, Orbital Welding, Stainless Steel Fabrication, Weld SugaringAug 12, 2021 4:07:52 PM
Comments