Choosing and Changing Orbital Welding Tungsten Electrodes
Tube and pipe fabricators need consistent and repeatable welds, especially with today’s high standards for the industry. What better way to do that than through mechanized gas tungsten arc welding (GTAW) systems. But, even automated processes can have varying results when your consumable products, ceriated tungsten electrodes, aren’t supporting your system properly.
If you are using generic orbital welding tungsten electrodes, you are putting your project at risk to several problems. GTAW systems require tungsten electrodes that can consistently create robust welds over a long lifespan. To optimize your orbital welding results, you need high quality ceriated tungsten electrodes.
So, what affects the longevity and quality of tungsten?
The proper chemistry, manufacturing and grinding process - aspects you only get when investing in premium level tungsten.
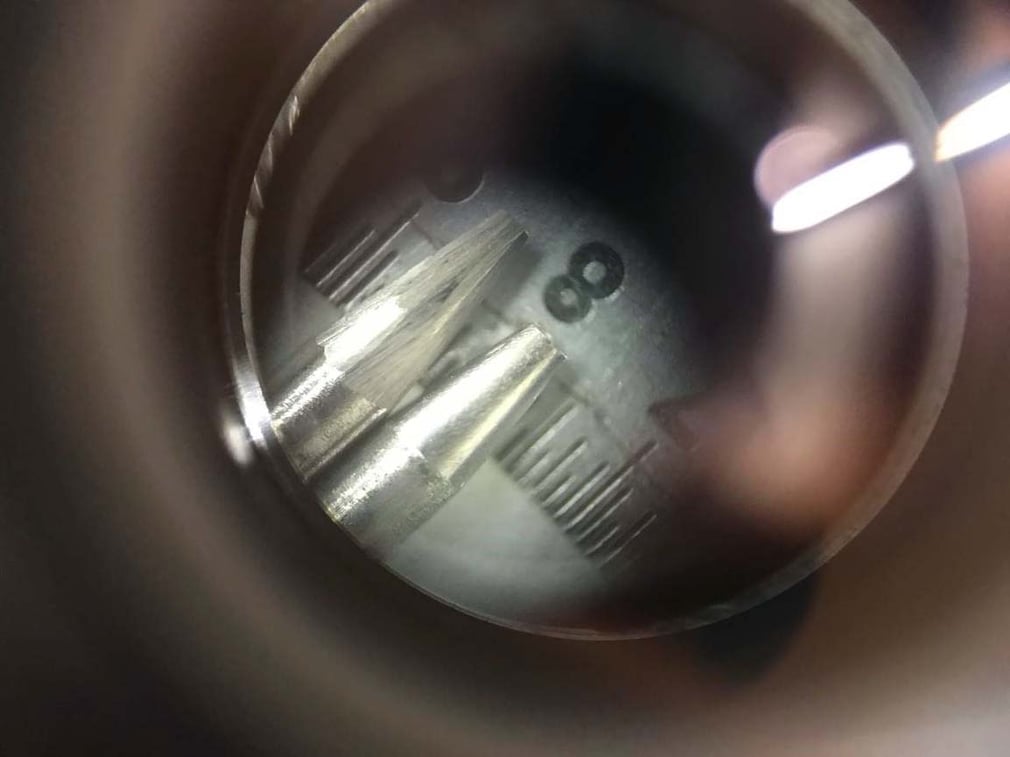
MIT Tungsten Electrode Manufacturing Process
We use 2% ceriated tungsten that meets ANSI/AWS A5.12-98 tungsten standards. All MIT tungsten is custom-cut and goes through our detailed manufacturing process, which includes precision grinding and polishing.
Some companies decide to have tungsten ground manually internally – which works for manual processes but isn’t ideal for automated GTAW systems due to the inconsistencies produced.
Every piece of MIT tungsten is precision-ground in house. We grind electrodes longitudinally and give them a flat tip to improve arc starting and create better arc control. It also works to prevent burrs and tungsten inclusions that cause rejects in many critical applications.
MIT tungsten is inspected with a microscope to ensure quality on every tip. Our process results in angle accuracy up to ± ½ degree and tip width within ± .003 in. We can also create custom orders at any length and degree, with a wide range of tungsten diameters from .040” up to .125”.
Lastly, our process ends with super-polishing each piece of tungsten to extend its life.
The Bottom Line - Price
While there are cheaper, generic options at your local welding supplier, they do not regulate or manufacture tungsten to meet ANSI/AWS high standards.
You may initially save money purchasing generic ceriated tungsten, but the repercussions of a faulty weld can end up costing your company valuable time and financial resources.
Changing Out Tungsten in Your Weld Head
If you purchase generic tungsten or grind in house, you need to be proactive in checking and changing out your tungsten electrodes. There are extra precautions to take when using lower grade tungsten.
Before you place tungsten in a weld head, make sure it is consistently ground. There should be no jagged edges or poor grind marks, and all tungsten should have similar angles and flat tips.
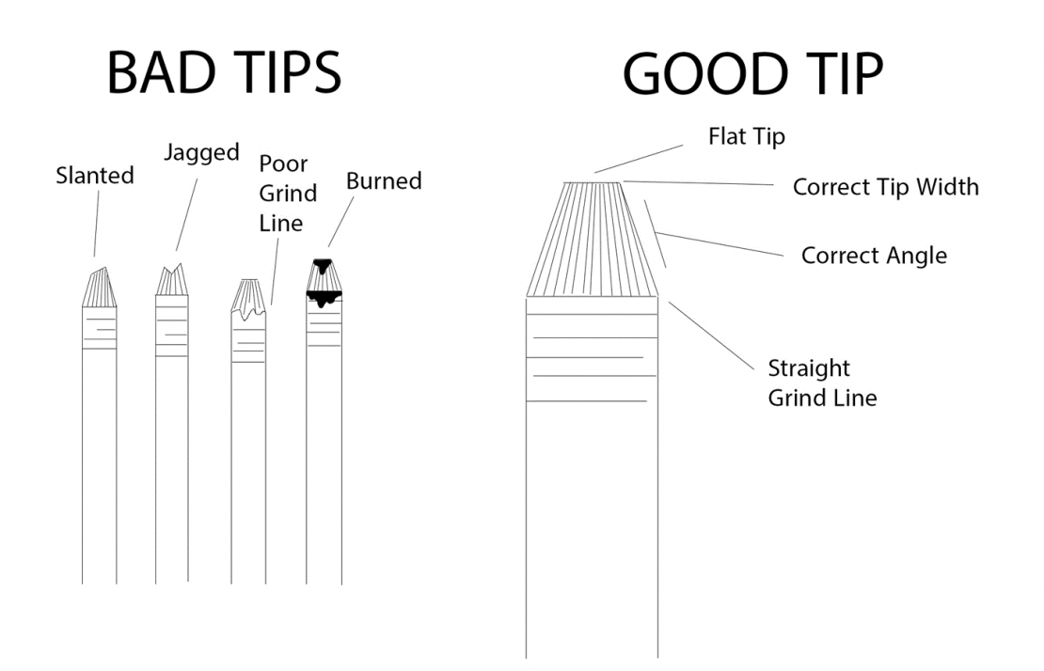
Test a weld. Is it straight and consistent? Does it have the proper width and bead size? If your weld isn’t up to standards, verify that you have the right electrode size and assess the quality of the product.
After you conduct an arc or weld, look to see if there is carbon build-up or burn marks. Misshapen, burned tungsten may be unusable.
Look for these signals to determine whether it is time to insert a new electrode.
Bad tungsten electrodes can end up costing your orbital welding project time and money. Avoid the risk and invest in a quality tungsten product. Contact a Morgan Industrial Technology representative today to discuss ceriated tungsten electrodes for your GTAW welding application.
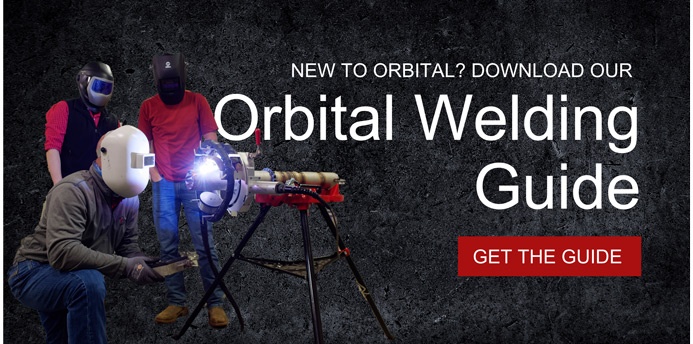
Sep 3, 2021 12:17:35 PM
Comments