Hygienic process facilities frequently need multiple outlets in a common distribution or collection manifold tube. This is a common requirement in food processing, pharmaceutical, and biopharmaceutical industries. One method for producing these manifolds is to form the branch connection mechanically out of the run tube using a pulled tee system invented by T-DRILL. These T-shaped extrusions are called T-pulls or collars. You may be wondering - what exactly are T-Pulls and can they be welded with an orbital welding machine?
Understanding Pulled Tees
An elliptical hole is first drilled in the manifold. Then, a spinning forming tool shapes the outlet extrusion. This is a commonly used process, important to industries manufacturing or installing high-purity systems under the ASME Bioprocessing Equipment (BPE-2019) code standards.
So, what is the benefit of using this technology? With a collar, only a single butt weld is required to connect the branch tube. This eliminates several additional welds that would otherwise be required, saving you both time and money.
Orbital welding can and should be used to make these critical welds, as this type of welding guarantees a smooth, fully penetrated, crevice-free ID bead.
The Key to Orbital Welding Pulled Tees
Orbital weld heads on the market typically use collets, which have been sized to the tube OD, to clamp the head firmly on both sides of the weld. The T-DRILL process can only create an extrusion with minimal or no straight length, meaning traditional collets cannot clamp onto the piece. In addition, the standard location of the tungsten electrode within a weld head is 0.75” (19mm) from the face of the collet, which would not allow the tungsten to be centered over the weld seam.
It is necessary to extend the tungsten out beyond the body of the weld head to reach the aligned weld joint. Magnatech’s solution requires the branch tube to be tack welded to the collar. Extended collets then are used on the branch tube side only. This improves the alignment and clamping of the head on the tube.
On the collar side is a gas shield, fabricated of a reinforced fiberglass tube, in order to keep inert argon gas inside of the head. These gas shields are fabricated for a specific header/manifold tube OD and collar OD. The end of the tube contacting the header is machined with a profile to match the OD of the header.

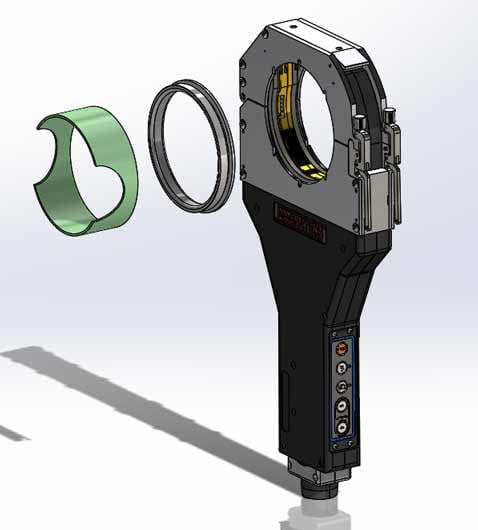
Note that the need to extend the tungsten often requires the use of a larger head model than would normally be required. The tungsten holder and tungsten are radiating high frequency/high voltage during arc starting. If the extended tungsten holder is too close to the head, it can arc over to the head (which of course is at workpiece ground potential). For example, the opening of a Magnatech 820 weld head 2” (50mm), will not allow the tungsten extender to be used on a 2” (50mm) tube, although it could be used on a 1” (25mm) tube.
The end-user frequently uses tape to positively seal the small gap between the gas shield and manifold tube. The material being welded is commonly 316L stainless steel, which must be purged to less than 25 ppm to avoid any oxidation.
When orbital welding tube and pipe tee collars and other specialized applications, look to Magnatech welding equipment for the solution. Contact MIT at (417) 485-4575 to learn more.
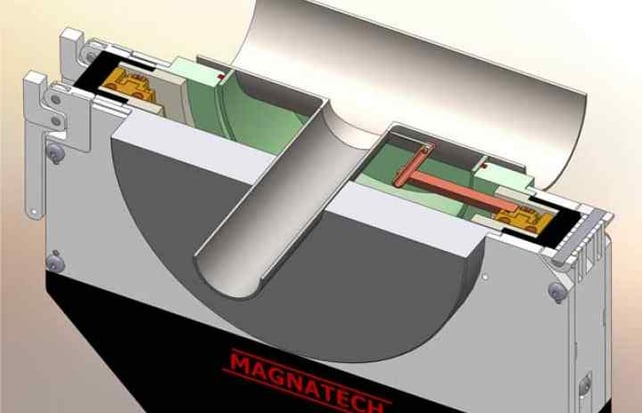
May 26, 2020 12:00:00 AM
Comments