As recently as a few decades ago, aerospace manufacturers had to rely on traditional welding methods to join pipes and tubing together. But with the advent of orbital welding, that has all changed. Orbital welding uses a rotating weld head to create a weld around the circumference of a pipe or tube, making for more consistent and reliable welds than traditional methods. Aerospace manufacturers have standardized orbital welding because it allows them to produce high-quality products quickly and efficiently. There are so many benefits to using orbital welding, but we’ve narrowed it down to the 5 that make orbital welding the most in demand type of welding.
Automated Welding Increased Productivity
There are many benefits of orbital welding, including:
Increased accuracy
Welding in tight spaces
Reduced rework
Improved productivity
Consistent and repeatable results
Programmable Welding Parameters
Consistent and Repeatable Results
The main advantage of orbital welding is that it is a very consistent process. Once the machine is set up, the weld will be the same every time. This is crucial in aerospace manufacturing, where parts must meet very precise specifications. A slight variation or incorrectly fused set of pipes can severely decrease the deliverability of liquids and gasses to critical components or spell disaster for the project.
Works In Confined Spaces
Another big advantage of orbital welding is that it can be done in confined spaces. This is often necessary for aerospace manufacturing, where parts are often close together. If the head of an orbital welder can reach around a pipe, it can complete the weld easily and efficiently.
Weld Smaller (Diameter matters)
Orbital welders can fuse some of the smallest tube in the world. When calibrated correctly, the orbital welding system can weld pipes and tubes as small as 1/8" (3.175mm). This is also vital in the production of some pharmaceutical application as orbital welding can range and be from 1/8" to 6.625". With such a wide range, the scope of projects can increase significantly, given you have the right weld head.
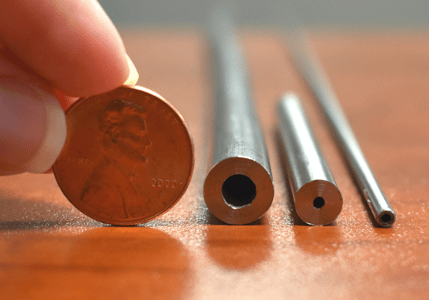
Certified Calibrated Equipment
MIT has partnered with the 2 biggest names in Orbital Welding (AMI & Magnatech) to offer certified calibrated power supplies and weld heads. Having a certificate of calibration is incredibly important to clients whose projects require incredible levels of precision and documentation. Our customers can confidently provide certified documentation that their equipment is operating at the highest caliber and has been inspected by some of the best techs in the industry.
Programmable Weld Parameters
Both AMI and Magnatech offer programmable weld parameters to cut down on having to calculate diameters, speed, arc gap, and amperage. These programmable parameters increase welders’ efficiency, cut back on mistakes, and help boost production by cutting down on punching in the same sequences over and over. Unlink Mig and Tig welding, having an automated weld head with a programmable system in place sets the welders up for repeatable success.
Aerospace manufacturing and Pharmaceutical Development has standardized orbital welding because it is a more consistent, reliable, and efficient method of welding. With the help of orbital welding, aerospace manufacturers can produce high-quality products quickly and efficiently. If you're in the aerospace industry and looking for ways to improve your welding processes or consider investing in an orbital welder connect with our Business Development Team at the link below.
Aug 26, 2022 10:33:09 AM
Comments