Even the most experienced welders can encounter issues with their orbital welding system. Our team of factory-certified repair technicians have years of practice repairing Arc Machines Inc power supplies and weld heads, and we want to share some of their valuable knowledge with you. Keep reading to learn the causes behind common faults and how to perform basic troubleshooting techniques on your AMI welding machine.
AMI Power Supply
Gas Fault
This fault occurs when a flow sensor is not reading a minimum of 3 CFH going through the weld head. To ensure the proper flow rate, check the flow meter and incoming gas. Often, the connecting gas lines from the adapter cable to the weld head will become disconnected to cause a gas fault.
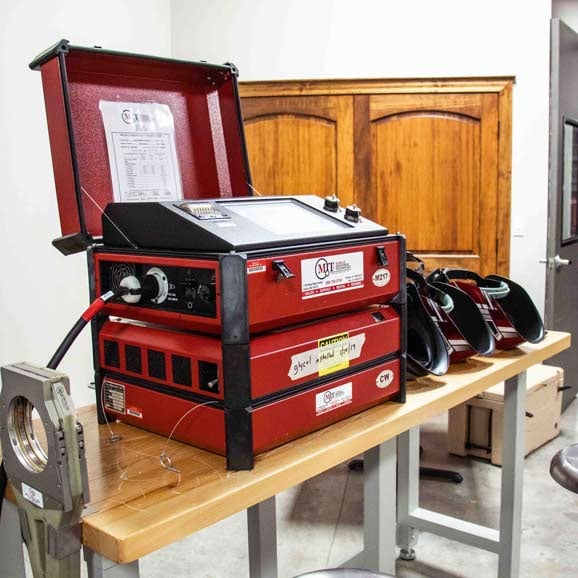
Coolant Fault
If the water cooler does not sense a minimum of .15 GPM passing through the flow sensor, this fault will take place. The cause could be the coolant in the tank is not filled enough for constant coolant flow rate or the intake hose is not submerged enough and is sucking air instead of coolant.
Also, check the male/female brass quick disconnects from the adapter cable to the weld head cable to make sure they are properly seated to allow coolant to pass between the two.
Stub Out Fault
This fault occurs normally when the tip of the tungsten touches the weld puddle and the arc can no longer be maintained. If your tungsten touches the workpiece or weld puddle, it will need to be changed out - the electrode is now contaminated. Consider adjusting the angle or tungsten position further away from the weld seam.
Input AC Fault
The input AC fault can happen due to two different reasons. First, the incoming power to the machine is not the same as what is selected on the side panel toggle switch. Example: AMI welding machine is set for 110V and someone plugs in 230V.
Second, the selected power supply program has a higher welding amperage than what the AMI welding machine is rated for. Example: AMI welding machine is set to 110V, which has a max welding AMP of 100 amps, but the program selected has a level 1 amperage set to 125A.
LVPS/TMP Fault
This fault indicates that the Low Voltage Power Supply and/or internal temperature on the PCB boards is having an issue. This could be an issue with the current control board, the 60V board or the interface board. This fault requires service from a factory-certified repair center to get up and running once again.
AMI Weld Heads
Bad Start
There are multiple reasons a bad start could occur. A piece of poor-quality tungsten could be a cause so make sure you are able to identify the attributes of good tungsten and when it is time to insert a new piece. Read our blog on choosing tungsten electrodes for more information.
Another reason for a bad start could be insufficient gas pre-purge. Insufficient gas pre-purge results in the AMI weld head trying to burn oxygen instead of inert gas (argon).
Alternatively, a poor cable ground or severed ground line inside the coolant line of the weld head could be the root cause of a bad start.
Rotor Spins Continuously
If the home limit switch is not engaging properly when the lobe of the rotor passes by it, the rotor will spin continuously. Adjusting the limit switch may help with this issue, but if not, it could be a broken wire in that part of the assembly. This calls for repair by certified professionals.
Weld Head Clamps Are Extremely Hot
This problem could be caused by the weld head not receiving enough coolant flowing through it due to blockage or swollen internal ground lines. If the coolant flow is too low, the power supply should throw the coolant fault. Sometimes reversing the flow rate to clear out a blockage will help; this can be done by switching the outgoing and return lines on the water cooler to backflush the coolant.
Conducting Orbital Welding Equipment Repairs
Now, you have the knowledge to identify the causes behind several common faults and can use basic troubleshooting techniques on your AMI welding machine. When dealing with a more involved fault or problem, please contact our repair center to troubleshoot over the phone or send in your equipment.
Do not attempt to repair or alter your orbital welding equipment without the guidance of a factory-trained service team member. Attempting your own repairs can result in more costly repairs. MIT always suggests calling a member of our team to see if your equipment needs to be sent in for repair.
Keep in mind that you should also send your orbital welding power source in for yearly calibration. Power source calibration and other preventative maintenance measures can help ensure the well-being of your equipment and prevent issues that may cause critical downtime at your job site.
Let MIT know how they can serve you and your AMI welding equipment. Contact us with any repair questions about your orbital welding equipment, facing tools, or orbital cutters.
May 18, 2020 12:00:00 AM
Comments